What we doAdvanced technology at the service of recycling
The AMP Recycling production lines operate with an installed recycling capacity of approximately 60,000 tonnes of post-consumer PET food packaging per year. The production lines boast cutting-edge equipment, like laser, infra-red and optical selection units that can guarantee the greatest efficiency. AMP is today a pole of excellence in recycling, which can convert post-consumer PET trays and bottles into high quality secondary raw materials that it then supplies to the ILPA Group companies and selected European customers. The AMP plant is certified EuCertPlast and EuCertPlast Food and it only procures from selected European suppliers. This allows us to maintain high product quality standards and guarantees the highest levels of safety for customers and consumers alike.
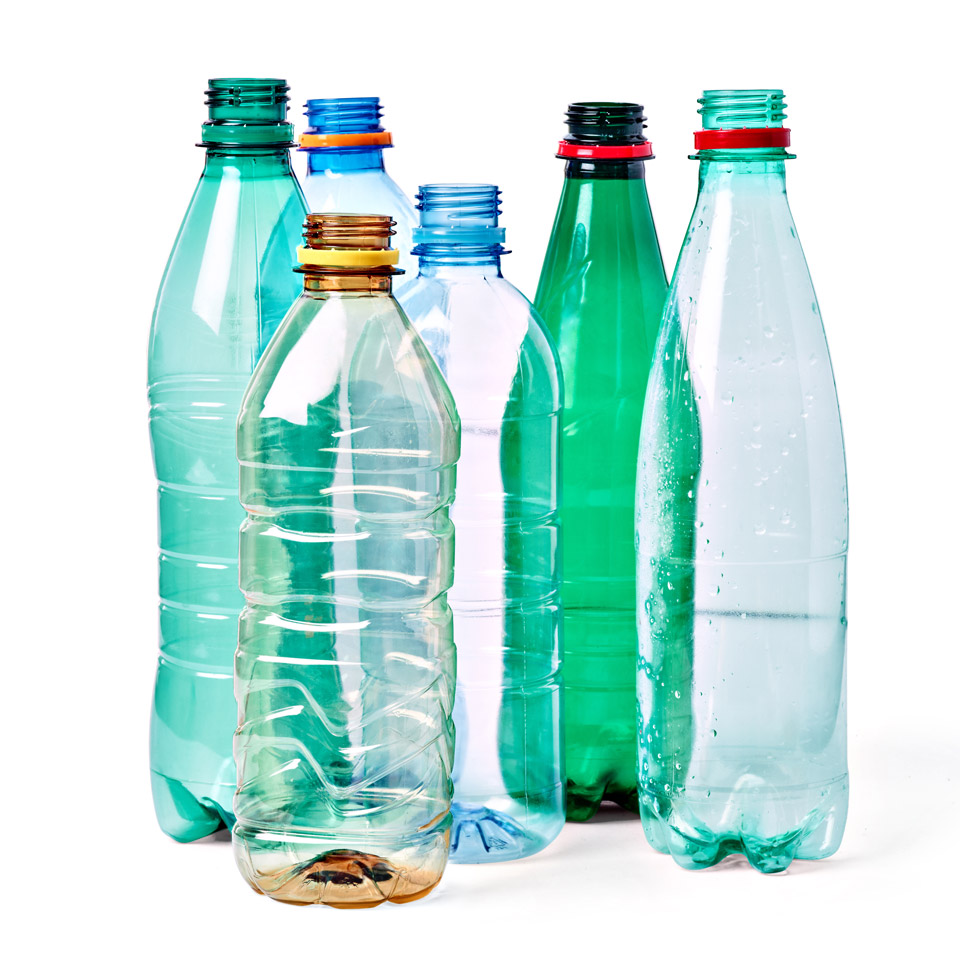
The production steps
Sorting
- Metal separation: ferrous and not ferrous
- Aeraulic separation for film
- Label remover
- Ballistic separation
- Polymers and colours detection (with laser sorting)
- Manual re-sorting
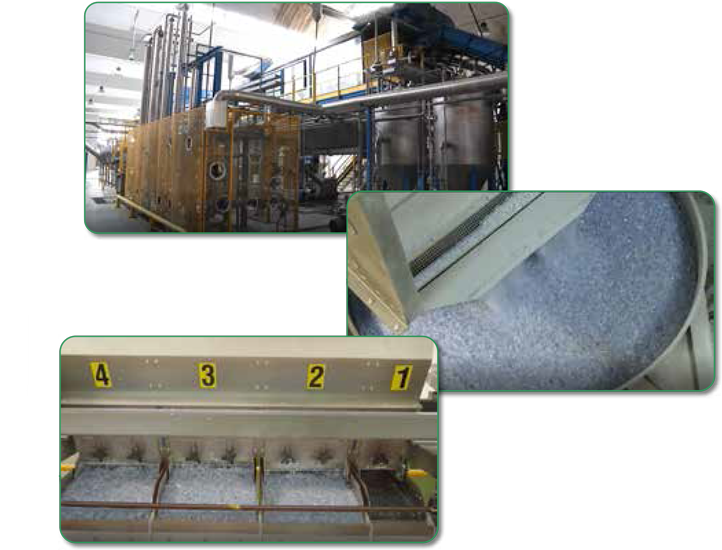
Washing
- Grinders
- Hot washing
- Swim-sink procedure
- Drying
- Mixing silos
- De-dusting
- Coarse-grit separation
- Flakes sorting: metals; polymers; colours
Packing Extrusion
- Flakes packaging
- Flakes extrusion
Once flake processing is complete, they are packaged into bags, ready for delivery. Alternatively, they can be sent directly to the extrusion lines for transformation into R-PET reels.
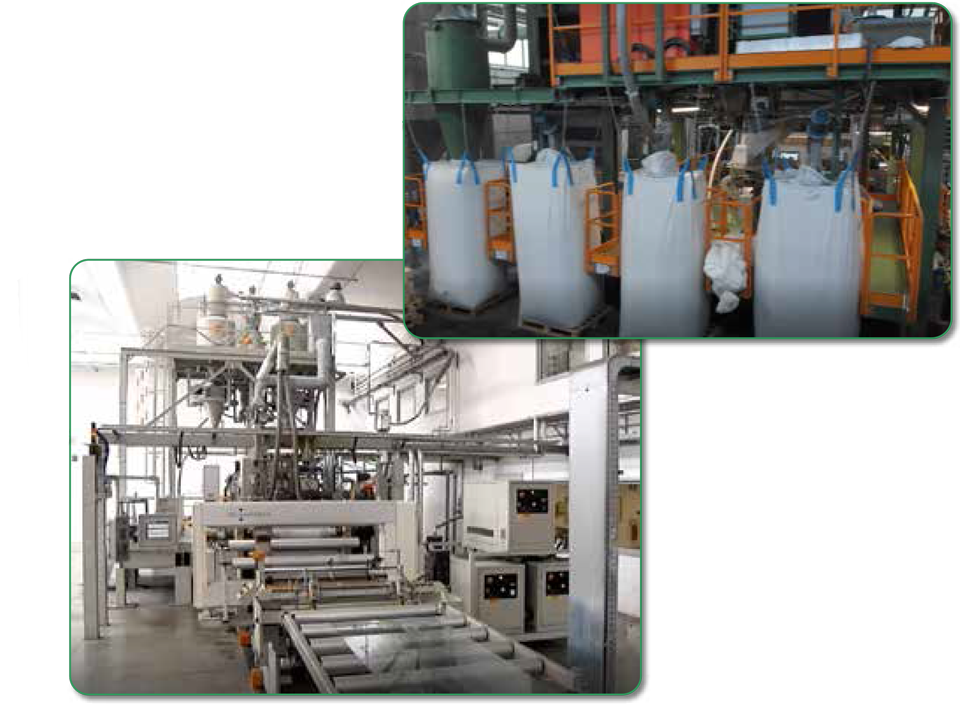
AMP: the added value
- Qualification of suppliers
- Control of the feedstock supply
- Constant quality checks and internal lab tests
- Quality of the input stream
- Control of the contaminant
- Continuity and consistency of supply
- High quality R-PET flakes
- EuCertPlast + EuCertPlast food certifications
- Control over the “superclean process“ for direct food contact: EFSA approved 100% R-PET
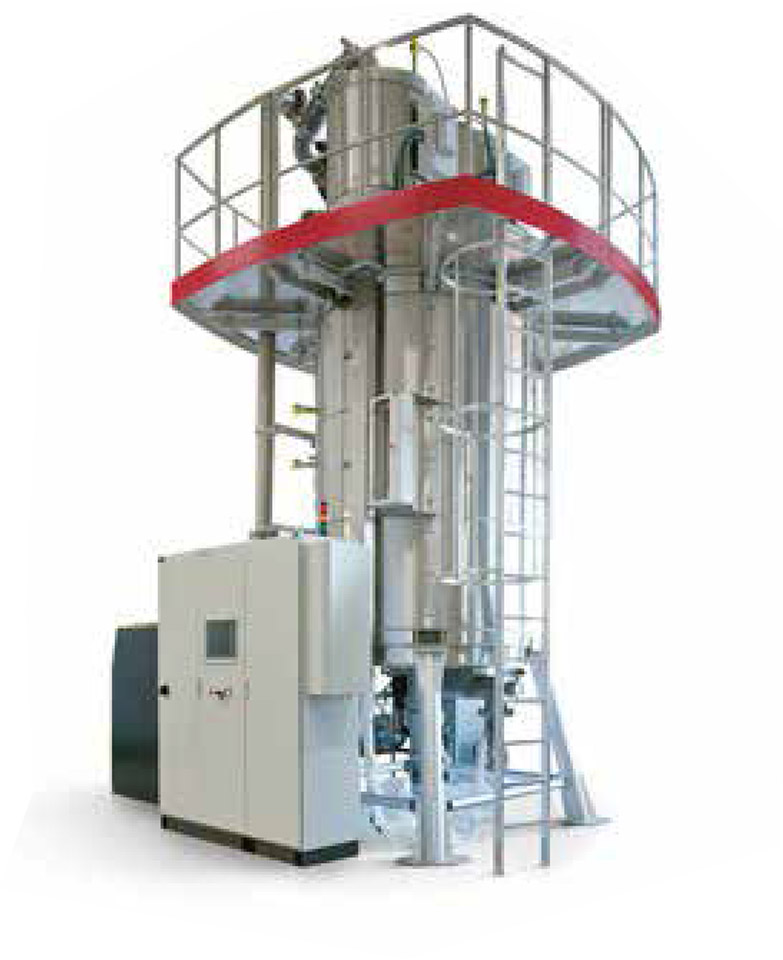